What Is Process Calibration?
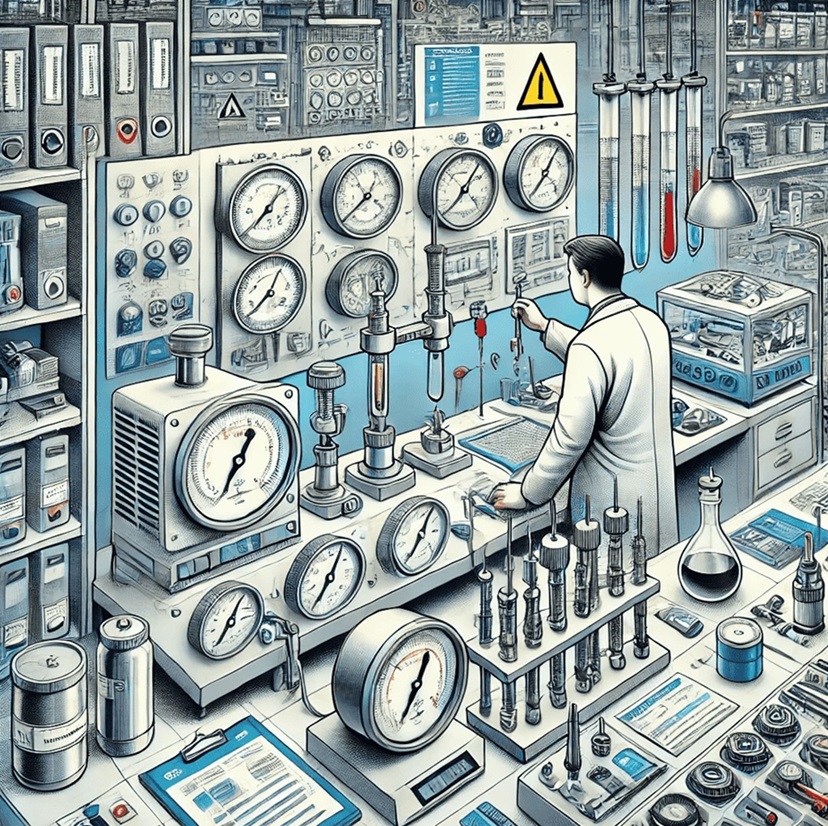
When delving into the world of process calibration, one must consider its profound impact on the precision and reliability of measurement instruments. In essence, calibration is the comparison of measurement values delivered by a device under test with those of a calibration standard of known accuracy. This practice ensures that the measurement instruments in question maintain their accuracy and performance within acceptable limits.
What Is Process Calibration?
When delving into the world of process calibration, one must consider its profound impact on the precision and reliability of measurement instruments. In essence, calibration is the comparison of measurement values delivered by a device under test with those of a calibration standard of known accuracy. This practice ensures that the measurement instruments in question maintain their accuracy and performance within acceptable limits.
The Fundamentals of Calibration
The calibration process begins with the design of the measuring instrument that needs to be calibrated. The design must be capable of maintaining calibration through its designated interval, ensuring that measurements remain within engineering tolerance when used under specified environmental conditions. Calibration involves several key steps:
- Comparison with Standards: The device under test is compared against a calibration standard. This standard is often traceable to national or international standards, such as those maintained by the National Physical Laboratory (NPL) in the UK or the National Institute of Standards and Technology (NIST) in the United States.
- Adjustment: If a significant error is detected during the comparison, adjustments may be made to correct the error to an acceptable level.
- Documentation: The results of the calibration process are meticulously documented, including any adjustments made and the measurement uncertainties involved.
The Importance of Calibration Services
Calibration services are crucial for several reasons. Firstly, they ensure the accuracy and reliability of measurement instruments, which is essential for maintaining the quality and safety of products and processes. In industries such as pharmaceuticals, aerospace, and manufacturing, precise measurements are vital to meet regulatory standards and ensure product quality.
Secondly, regular calibration helps identify and rectify any drift or degradation in instrument performance over time. This proactive approach prevents costly downtime and potential safety hazards caused by inaccurate measurements. Furthermore, calibration services provide traceability, ensuring that measurement results are consistent and comparable across different locations and time periods.
Modern Calibration Processes
In today’s globalised world, the need for consistent and comparable standards internationally has led to the establishment of national laboratories. These institutions maintain primary standards of measurement, which are used to provide traceability to customers’ instruments through calibration. Examples of such institutions include the National Metrology Institutes (NMIs) like the NPL, NIST, and the Physikalisch-Technische Bundesanstalt (PTB) in Germany.
Quality Management and Traceability
Quality management systems, such as ISO 9001 and ISO 17025, require effective metrology systems that include formal, periodic, and documented calibration of all measuring instruments. These standards emphasise the importance of traceability to internationally defined measurement units, which is achieved through formal comparisons to standards. This traceability ensures that calibration results are accepted by outside organisations and supports regulatory compliance.
Calibration in Practice
Calibration may be required for various reasons, such as when a new instrument is purchased, after an instrument has been repaired or modified, or after it has been moved to a new location. It is also necessary after a specified time period or usage interval, before and after critical measurements, or after an event that might have compromised the instrument’s calibration, such as exposure to shock, vibration, or physical damage.
The calibration process for a specific instrument involves several steps, starting with a basic damage check. Some organisations collect “as-found” calibration data before any routine maintenance is performed. After maintenance and addressing any detected deficiencies, an “as-left” calibration is performed. This ensures the instrument is in optimal condition for accurate measurements.
Historical Context and Development
The origins of calibration can be traced back to ancient civilizations, where systems of measurement were developed to support commerce and technology. The term “calibration” itself likely originated during the American Civil War, related to the measurement of artillery calibre. Over time, calibration techniques evolved, with significant advancements during the Industrial Revolution.
One of the earliest pressure measurement devices, the mercury barometer, invented by Evangelista Torricelli in 1643, exemplifies the evolution of calibration methods. As technology advanced, more practical and accurate calibration instruments, such as the Bourdon tube, were developed. These indirect reading instruments became essential for high-pressure applications, furthering the precision of measurements.
Conclusion
Remember, the key to accurate and reliable measurements lies in regular calibration. This practice is essential for maintaining the integrity of your measurement instruments, ensuring safety, and meeting compliance standards in your operations. Trust in professional calibration services to uphold the highest standards of precision and reliability.