Understanding the Types of Encoders for DC Motors
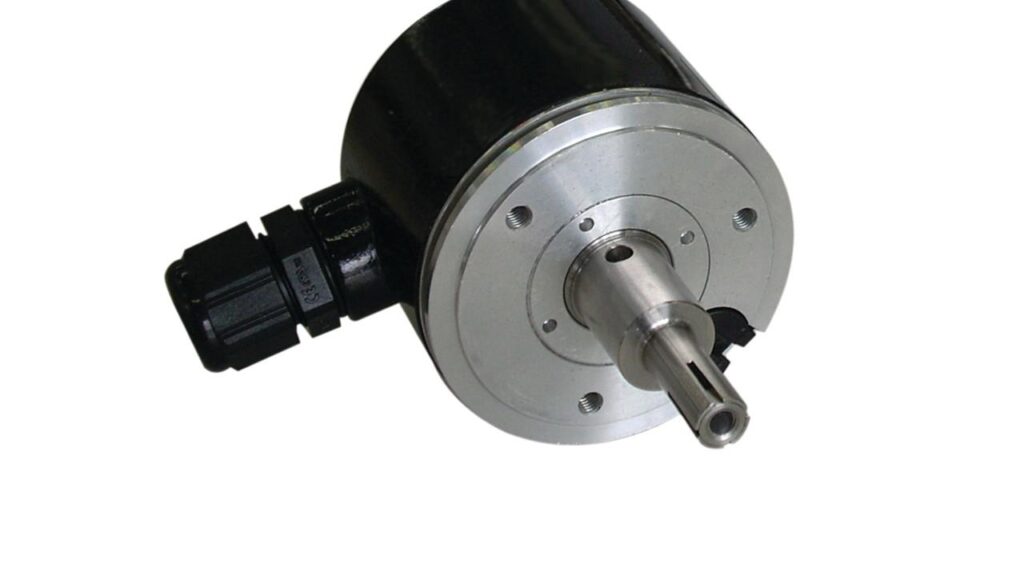
An encoder usually seems insignificant at first glance. However, it has a big role to play in a DC motor as it decides the speed control feedback and also the position in the motor shaft. This is why it becomes important for all to choose the right type of encoder for DC motors.
That being said, the types of encoders are more than one can imagine. From Optical Rotary encoders to Linear encoders, there is a wide variety that one can use for the motor. This is why we work on helping you choose the most suitable encoder for the process. We will delve into a few different types that will ultimately help you understand the specifications of it.
Understanding an Encoder for DC Motor
An encoder is a simple device that helps in measuring speed and position. This device is also used for tracking the rotational speed and direction of the DC motor, which is exactly what we are focusing on. These are seen in closed-loop systems where maintaining the position becomes extremely important.
There are two types of encoders used for a DC motor, Incremental and Absolute. However, these are also divided into different types like Incremental Rotary encoders, Magnetic encoders, and others. All these can be used in a DC motor. These vary in the technology that is used for detecting motion and position.
Types of DC Motor Encoders
If you proceed to search the market, then you will find that there are many types of DC motor encoders like Optical Rotary encoders and others available. All of these types come with their unique set of benefits for specific applications. We have listed out a few types of encoders that you can consider choosing.
1. Incremental Rotary Encoders:
This type of encoder is widely used in places where there is a need for monitoring speed. On top of that, it also helps in understanding the direction of the motor. Incremental Rotary encoders are exceptionally well suited for measuring the position changes. Plus, it also helps in tracking the speed of the rotating shaft. This one converts the position or angular motion of a shaft into a digital or analogue code. After that, the code is used to identify the position or motion. This is undoubtedly one of the commonly found types of rotary encoders in the market.
One can easily find an Incremental Rotary encoder in applications where there is a need to monitor the motor’s speed. From packaging to printing, all industries use this one. Other than that, you can also find it in the transportation industry.
2. Magnetic Encoder:
This type of encoder uses the power of a magnet that is attached to the shaft of the motor. After that, the magnet is read with the help of a magnetic sensor that works by producing an electrical signal. Next, the signal is converted into an analog or digital signal, which works on producing cosine and sine waves. Sometimes it can also produce square waves depending on whether the encoder is absolute or incremental.
This encoder has its place in different types of applications such as monitoring motor activities and measuring speed. On top of that, this one can easily be sized based on the project which often makes it ideal for many applications. However, remember that this can be interfered with from outside sources like other electronic devices.
3. Optical Rotary Encoder:
This type of encoder uses the power of light for its function. The light is supposed to shine with the help of a coded disk for tracking the shaft’s movement. The feedback that you get from the encoder is received based on the interruption of light. These ones are ideal for offering high-precision accuracy and also come with reliable application.
Optical Rotary encoders are versatile in nature. This is exactly why their application can be found in different types of industries. For instance, you will be able to find these in industrial automation and controls where accurate position feedback and process control play a big role. Other than that, you will also be able to find these in aerospace and defence applications like aircraft control systems. This helps in offering precise feedback for positions and speed in those applications.
4. Linear Encoder:
This one is the most widely used type of encoder, like the Incremental Rotary encoder. This one uses a magnet or a fixed light, which is fixed to a transducer or any other type of sensor for detecting position changes. This one has a few slots that are situated in the plates of the linear encoder. These are the very things responsible for letting in light, which in return sets off the transducer.
The transducer proceeds to produce a signal for output that is proportional to the position change. The best thing about this encoder is that its design is quite simple, which helps in its wide application in places like printers and assembly lines.
5. Angle Encoder:
This one is one of those encoders that is commonly found in the industry. Angle encoder uses a wheel or disk that is placed on the motor’s shaft. The disk comes with a few markings which are read with the help of an optical sensor. This process in the end creates an electrical signal. The type of encoder is also great for measuring the changes in the load.
However, one thing that sets it apart from most encoders is that it can also provide the starting and the final absolute position of the load. This is a simple way in which it provides accurate data. One can easily find this encoder in different types of applications like position feedback, motor control, and others.
Conclusion
Choosing an encoder can be tough, especially when there are multiple options like Optical Rotary encoders and others. This is why, through this blog we worked on simplifying the process for you. We discussed a few types of encoders and their specifications. We are sure that this will definitely help you a lot.